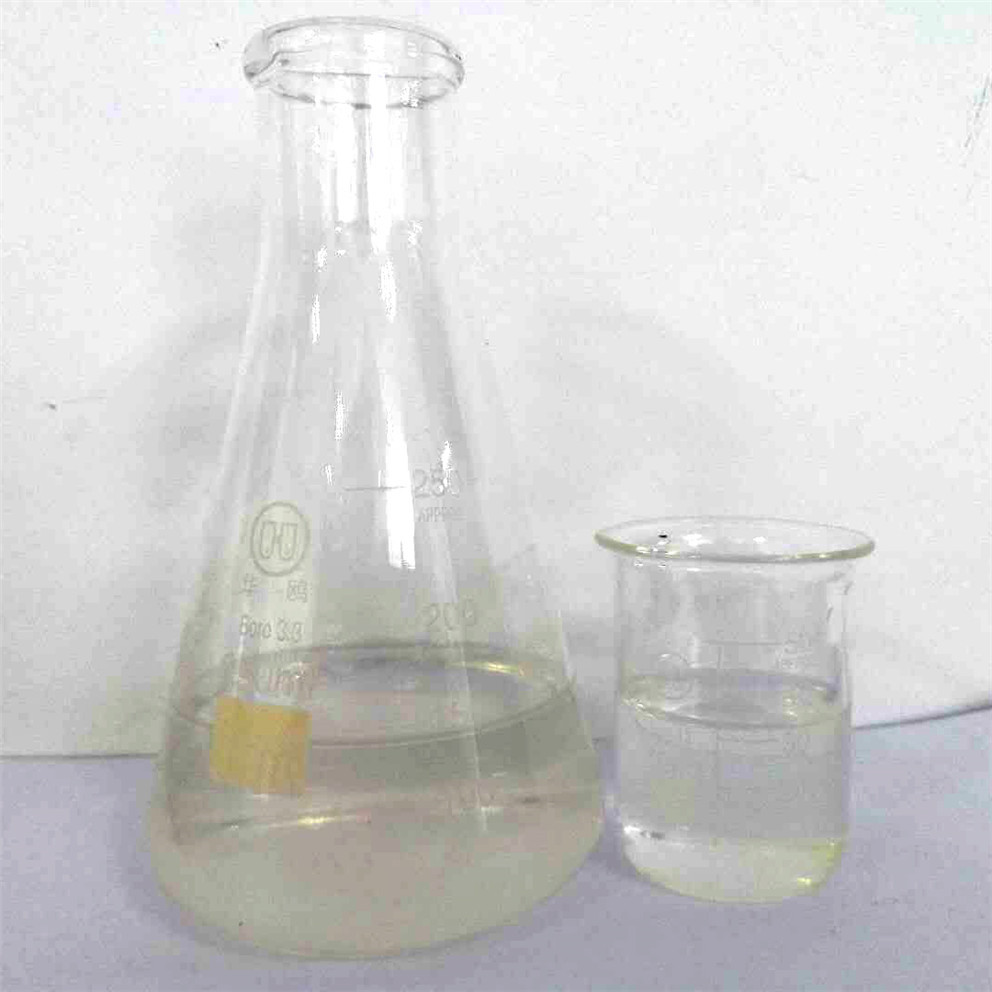
Any product tends to homogenize in continuous market competition, and buyers are happy to see sellers suffer greatly. The trend towards homogenization is precisely what the market needs, which means that after a long period of trial and error, the product has gradually found the most suitable template for a wide audience of customers. Afterwards, the procurement has gained a certain ability to distinguish the quality of the product. The seller can no longer profit from the buyer's trial and error through so-called "differentiation".
However, even the most homogeneous products will have directions for optimization according to different regions. The mother liquor of water reduction also conforms to this characteristic. The synthesis process of polycarboxylate water reducing mother liquor is similar nationwide, and even different catalysts can ultimately obtain mother liquor with a similarity of 90% or even 95%. Based on the current situation, the difference in raw materials for additives in different regions can be completely compensated for through cost or adding small materials, without causing significant differences in user usage. Even if industry leaders can achieve differentiated mother liquor, they have not thought of one mother liquor formula for each region.
This article is only to introduce whether there are other adjustment methods that can better meet the needs of different regions, and there is no distinction between superiority and inferiority.
There are many directions to change the mother liquor process, including temperature, oxidation-reduction agent, chain transfer agent, stirring and dripping time, acid ether ratio, acid feeding method, and material concentration at the bottom of the reaction vessel. Among them, the acid to ether ratio and acid feeding method have the greatest impact or personal experience of differentiation.
The ratio of acid to ether is often used in many literature to convert it into a certain amount of substance, and then adjusted accordingly. This is a standardized operation during the initial stage of product research. Now that there is a reasonable ratio of acid to ether, I prefer to change the ratio directly and clearly, which is the proportion of one ton (one kilogram) of mother liquor. Acrylic acid: monomer=40:340 is a commonly used ratio. Increasing the amount of acrylic acid can improve the water reduction rate of the mother liquor, but excessive amounts of acrylic acid can lead to a decrease in the slump retention performance of the mother liquor. In sales, in order to lower the selling price, it is often considered to lower the product cost. Increasing the dosage of acrylic acid on the basis of acrylic acid: monomer=40:340 will lead to an increase in the solid content of the mother liquor, thereby increasing costs. A simpler and more crude operation is to directly reduce the monomer dosage, while keeping everything else unchanged. For example, changing acrylic acid: monomer=40:340 to acrylic acid: monomer=40:330 or even acrylic acid: monomer=40:320. This operation is deeply loved by many manufacturers. The buyer reduces the price and the profit remains unchanged, while the seller saves money and has a similar water reduction rate, making it enjoyable and enjoyable. When polycarboxylate mother liquor was first launched, the standard solid content was generally 40%. However, through continuous competition and price reduction, the solid content of mother liquor in the market is still 40% through verbal communication. In fact, most of them are only 38.5% or even lower.
In addition, I also found an interesting way to change the performance of the mother liquor during my experiments.
The only difference between the above two synthesis methods is the addition of 8% A material solution in one go before the reaction. There is no difference in water reduction rate between the mother liquor synthesized by these two processes. The net slurry test is also similar. However, there are significant differences in concrete adaptation. The concrete slurry adapted to the mother liquor with pre added 8% A material is light and non bleeding, but has poor workability. The surface of the concrete, like bread, lacks luster. As the amount of pre added acrylic acid increases, the water reduction rate can be improved, but the negative effects are greater. At least the materials are not suitable for my local area. I found in the experiment that another catalyst process is actually more suitable for the operation of pre adding A material.
There is room for modification in the existing mother liquor synthesis process, but it is not significant. By optimizing, it can better adapt to local concrete materials. Exploring in this direction is an advantage for additive manufacturers in various regions, and foreign manufacturers will not transfer their technology to every mixing plant. Friends who want to save costs can try to find some advantages directly in small differences.