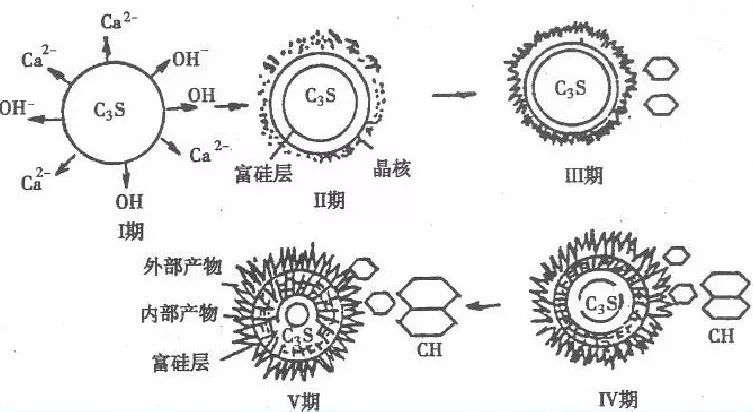
The birth of concrete can be traced back to the Pantheon built by the ancient Romans 2000 years ago. The foundation, walls, and dome of the Pantheon are all made of concrete poured from volcanic ash. However, with the level of technology at that time, people still couldn't understand why volcanic ash could provide stone like strength. It can be considered as an exclusive skill point prepared by God for the ancient Romans. Volcanic ash was rarely encountered in ancient China. Unfortunately, the ancient Romans did not continue to study this skill. In the long days that followed, the technology tree of cement was never reignited. Until 1756, British engineer J. Smith discovered in his study of the hardening properties of certain lime in water that in order to obtain hydraulic lime, it was necessary to use limestone containing clay (which is now the main raw material for cement) for firing. This important discovery laid the theoretical foundation for the development and development of modern cement. In 1824, British construction worker Joseph Aspdin invented cement and obtained a patent for Portland cement. He uses limestone and clay as raw materials, mixes them in a certain proportion, and then calcines them into clinker in a vertical kiln similar to lime, which is then finely ground to produce cement. It is named Portland cement because its color after hardening is similar to the stones used for construction in Portland, England. It has excellent architectural performance and epoch-making significance in the history of cement. In the 20th century, while continuously improving the performance of Portland cement, people successfully developed a batch of cement suitable for special construction projects, such as high alumina cement, special cement, etc. More than 100 types of cement have been developed worldwide, with an annual cement production of approximately 2 billion tons in 2007. In 1952, China formulated the first national unified standard, which established the principle of multiple varieties and grades in cement production. Portland cement was renamed silicate cement based on its main mineral composition, and later renamed Portland cement to this day.
The product obtained after mixing, calcining, and grinding limestone and clay in proportion is Portland cement. However, with further research on cement. By adding a certain amount of mixed materials (mineral powder, fly ash) and an appropriateamount of gypsum to Portland cement, certain characteristics of the cement can be improved. The addition of gypsum can prevent the instantaneous setting phenomenon of cement. Therefore, pure Portland cement is generally referred to as clinker. The author estimates that as long as one is not a cement practitioner, the vast majority cannot come into contact with pure clinker.
Clinker+admixture (6% -15%)+gypsum (1.8% -2.5%)=ordinary Portland cement.
The most commonly used commodity concrete company is P ▪ O 42.5 cement refers to ordinary Portland cement with a compressive strength of 42.5 MPa at 28 days.
Due to the small amount of mixed materials, the properties of ordinary Portland cement are basically the same as those of Portland cement, with slight differences mainly manifested in: slightly lower early strength; Improved corrosion and heat resistance; The heat of hydration is slightly lower; The frost resistance, wear resistance, and carbonization resistance have slightly decreased.
The chemical reaction between cement and water is called cement hydration. I demonstrate the production and hydration process of cement using graphical methods.
Tricalcium silicate, dicalcium silicate, and water react to form hydrated calcium silicate. It is relatively easy to understand. The reaction process of tricalcium aluminate and tetracalcium ferroaluminate under the action of gypsum is relatively complex. Let me use a diagram to introduce it. In short, various hydrates have been generated. The cement hydration reaction is a continuous process that can be divided into five stages: 1. Induction period; 2. Acceleration period; 3. Decay period; 4. Stable period.
Inducing a rapid reaction in the early stage of cement, tricalcium silicate (C3S) dissolves in water and rapidly undergoes hydration and hardening, resulting in the first exothermic peak, which lasts for a short time and ends within 15 minutes. Afterwards, the response during the induction phase is extremely slow, also known as the quiescence phase. Generally lasting for 1-4 hours. It is the reason why the silicate cement slurry can maintain plasticity within a few hours. The reasons for the occurrence of a quiescent period include the protective layer theory and delayed nucleation theory, which induce the rapid production of hydrated tricalcium silicate in the early stage to cover the surface of cement particles, preventing further contact between water and cement. The initial setting time is basically equivalent to the end of the induction period.
The reaction during the acceleration period accelerates again, and the cement particles in the stationary period are exposed again and come into contact with water molecules due to the rupture of the protective film (hydrated calcium silicate). The second exothermic peak appears, and when it reaches its peak, this stage usually ends within 4-8 hours. At this point, the final setting has passed and hardening is beginning. The theory of delayed nucleation is that when tricalcium silicate comes into contact with water, it rapidly hydrolyzes, and calcium ions and hydroxide ions enter the solution. This turns the original surface of tricalcium silicate into a "calcium deficient" or "silicon rich" surface layer, and the calcium ions in the liquid phase will adsorb onto the silicon rich surface through chemical adsorption, making the surface positively charged. The high concentration of calcium ions on the surface of tricalcium silicate reduces the further hydrolysis of cement, thus forming a stationaryphase of the induction period. Calcium ions and hydroxide ions dissolve successively at a low rate, and when the liquid phase becomes supersaturated relative to calcium hydroxide, calcium hydroxide crystal nuclei rapidly form. During the growth of calcium hydroxide crystals, the calcium ions and hydroxide ions in the solution will decrease, resulting in an accelerated recovery period for hydration. The protective layer theory and delayed nucleation theory are currently in a controversial stage.
The stage in which the reaction rate decreases over time during the decay period is due to the obstruction of the hydration process of tricalcium silicate (C3S) as hydrates aggregate around cement particles, leading to a transition from an acceleration process to a deceleration process. For approximately 12-24 hours, hydration gradually becomes controlled by diffusion rate.
The reaction rate during the stable period is very low. The initial product, hydrated calcium silicate, grows on the surface of cement particles. Afterwards, water molecules need to pass through this layer of hydrated calcium silicate to enter the interior of the particles and continue to react with unhydrated tricalcium silicate. The hydration reaction is completely controlled by diffusion rate.
The final hardened cement slurry is a heterogeneous multiphase system composed of various hydration products and unhydrated clinker, solid phases, voids, water and air present in the voids. The hardened cement slurry is a porous body composed of solid, liquid, and gas phases coexisting. The relative content of various hydration products is: C-S-H gel (hydrated calcium silicate) accounts for 70%, Ca (OH) 2 accounts for 20%, ettringite and single sulfur hydrated calcium sulphoaluminate account for about 7%, and incomplete hydrated residual clinker and other trace components account for about 3%.
Compared to the hydration process of calcium silicate, the reaction process of tricalcium aluminate and tetracalcium ferroaluminate after adding gypsum is more complex. The reaction mechanism of cement can help us deeply understand the plasticity of concrete, the principle of slump loss, initial setting time, concrete cracking, etc. The principle of concrete admixtures also revolves around the process of cement hydration. For example, the water reducing mechanism of admixtures is that polycarboxylic acid molecules adsorb on the surface of cement particles, using charge repulsion and steric hindrance to prevent contact between cement particles and release water molecules that coagulate between cement particles. The theory of retarders is that the molecules adsorbed on the surface of cement particles chelate with calcium ions, hindering the formation of calcium hydroxide.