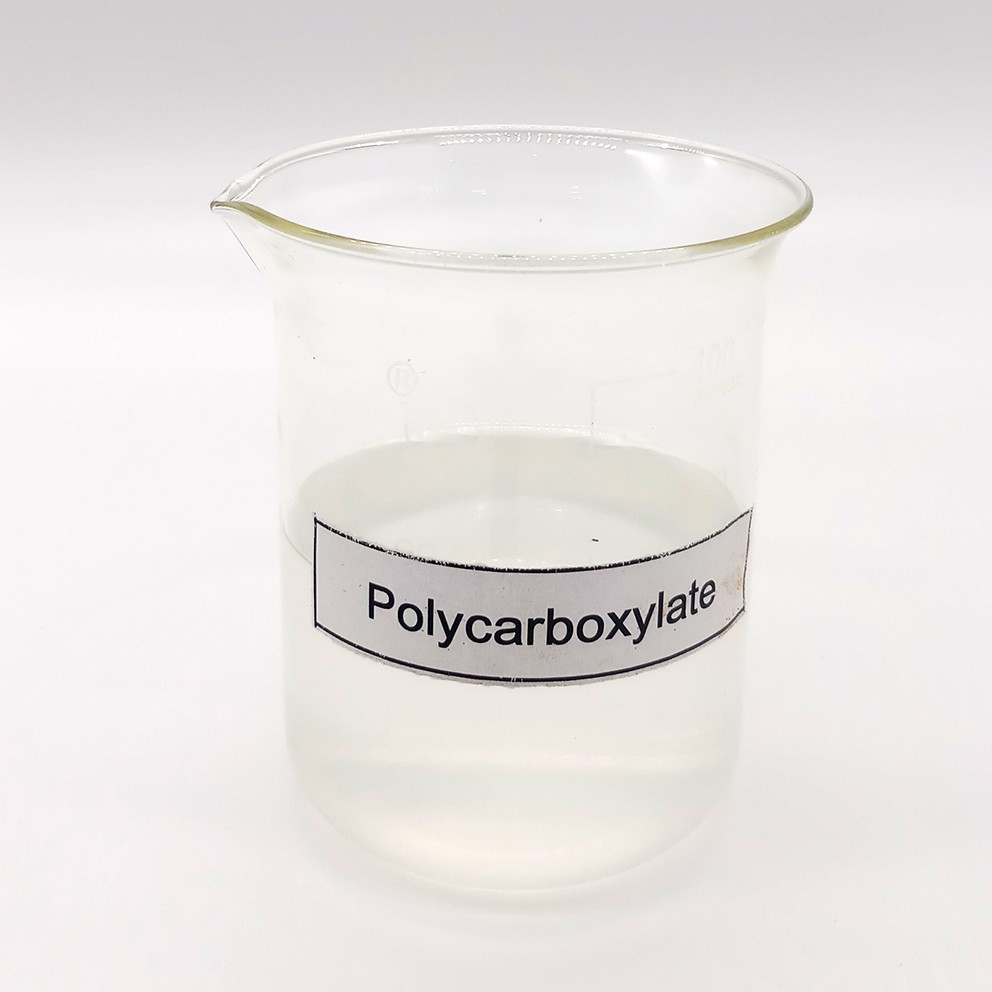
With the rapid development of China's economy and the improvement of construction level, the market has increasingly high requirements for the quality of concrete. The reduction of high-quality sand and gravel raw material resources and the complexity of concrete composition have always posed a major challenge to the slump loss of fresh concrete in engineering construction, especially since prolonged transportation can lead to excessive slump loss and affect the workability of concrete. Adding water to reshape the construction site will greatly reduce the actual strength and durability of concrete, such as impermeability, and also damage the workability and uniformity of concrete. Increasing the dosage of water reducing agent in the initial stage will cause segregation and bleeding of concrete, and the size of the dosage is also difficult to control. Too little usage does not meet the requirement of compensating for losses, and too much usage will result in concrete being transported to the construction site in a state of segregation and bleeding. Adding water reducing agents to reshape concrete before construction can restore its good working performance, but the difficulty in controlling the dosage can also cause segregation and bleeding of the concrete, damage the uniformity of the concrete, and result in differences in the strength of various parts of the concrete, reducing its flexural and compressive strength. A common method to improve the slump loss of concrete is to increase the amount of retarder components, but sometimes the problem of excessive retarder in concrete has not been effectively improved.
Slow release polycarboxylate water reducing agent is a chemical method that controls the dispersion process of water reducing agent molecules on cement particles, enabling the water reducing agent molecules to continuously disperse and slowly adsorb on the surface of cement particles within a certain period of time. Slow release water reducing agents can be divided into two types based on their release principles: physical release and chemical release. Physical sustained-release is mainly achieved through diffusion and permeation, such as using ice to freeze a portion of the water reducing agent and releasing the water reducing agent molecules by increasing the temperature and melting the ice. This method poses great difficulties in practical use. Chemical sustained release is achieved through the breaking of chemical bonds between atoms to achieve its principle of sustained release. Chemical slow-release water reducing agents can be divided into two types: intramolecular reaction type and cross-linked type. The molecules of intramolecular reactive slow-release water reducing agents generally contain amide groups, acyl anhydrides, and ester groups that can be hydrolyzed into hydrophilic groups such as carboxylic acids in alkaline environments. During the gradual hydrolysis process, these hydrophilic groups continuously adsorb and disperse cement particles. Crosslinked slow-release water reducing agents can directly introduce monomers with multiple double bonds through polymerization reactions or trace crosslink already polymerized macromolecules. They can also be ion crosslinked through coordination bonds formed between oxygen and metal elements on carboxyl groups. Similar to intramolecular reactions, cross-linked slow-release agents also gradually release dispersed macromolecules through hydrolysis in alkaline environments to achieve slow-release effects. The sustained-release mother liquor can be simply understood as the common cold capsules or sugar coated tablets taken in daily life. Some drugs that require small intestine absorption to avoid gastrointestinal absorption, the gradual dissolution of the sugar coating plays a role in the sustained-release effect, protecting the maximum absorption of drug components.
The slow-release polycarboxylate water reducing agent introduced below is chemically modified on the basis of the water reducing mother liquor. Introducing carboxylic acid derivatives provides initial protection for carboxylic acid ions in molecules. Due to the alkaline environment formed during the hydration process of concrete slurry, carboxylic acid derivatives in slow-release water reducing agent molecules undergo hydrolysis reaction during the concrete mixing process, gradually releasing carboxylic acid ions with anchoring effect and exerting dispersion effect, thereby achieving the effect of slowly dispersing cement particles. The application of slow-release mother liquor effectively improves the sensitivity of polycarboxylate admixtures to concrete raw materials and enhances their adaptability to concrete. The commonly used group for protecting carboxylate ions is the ester group, and hydroxyethyl acrylate is the most commonly used raw material for producing slow-release mother liquor. Because the initial water reduction rate of slow-release mother liquor is reduced compared to that of water reducing mother liquor, it often requires an additional cost in application. This is a significant obstacle for the practical application of slow-release mother liquor.
1、 Experimental raw materials
TPEG has a better slump retention effect, but for production convenience, the same monomer HPEG as the water reducing mother liquor was still used in this experiment. In the future, we will introduce the use of TPEG to synthesize polycarboxylate mother liquor. There is not much introduction to synthesis equipment. If you want to know more, you can refer to previous articles.
1. Monomer HPEG; Produced by Zhongshan Chemical in Fujian. Molecular weight 2400
2. Acrylic acid; Produced by Wanhua Chemical
3. Hydroxyethyl acrylate; Produced by Shandong Derui
4. Mercaptoacetic acid; Imported from Japan
5. Vitamin C; Produced by Shiyao Group
6. Hydrogen peroxide 27.5%; Local purchase
2、 Synthesis process and operation
The synthesis process and water reducing mother liquor are basically the same.
1. Start stirring and add 325g of monomer and 300g of water into a four necked bottle; Weigh 2.6g of hydrogen peroxide for later use (put it into four bottles before adding);
2. Weigh 25g of acrylic acid, 29g of hydroxyethyl acrylate, and 50g of water in beaker A; Weigh 0.5g of vitamin C, 2.6g of mercaptoacetic acid, and 50g of water in a beaker B;
3. After stirring for 30 minutes in a four necked bottle, most of the monomers dissolve in water. Pour the previously weighed hydrogen peroxide into the four necked bottle and continue stirring at the mixing station for 2 minutes;
4. Turn on the peristaltic pumps A and B, ensuring that the solution in beaker A is fully added within 120 minutes and the solution in beaker B is fully added within 150 minutes.
5. After the dripping is completed, continue stirring for 60 minutes and then add 192g of water;
6. Synthesis completed.
3、 Summary
Hydroxyethyl acrylate is the key to synthesizing sustained-release slump retention mother liquor. At the same time, the initial water reduction rate and slump retention effect of the mother liquor can also be adjusted based on the dosage of acrylic acid and hydroxyethyl acrylate. Relatively speaking, as the amount of acrylic acid decreases and the amount of hydroxyethyl acrylate increases, the initial water reduction rate of the mother liquor will decrease, and the slow-release performance will improve. The initial water reduction rate of the synthesis process mother liquor mentioned in the article is approximately 75% of that of the water reducing mother liquor, and overall, the slow-release effect is not very strong. For areas that do not require such high collapse protection effects, the cost-effectiveness will be higher when applied. As mentioned earlier, slow-release mother liquor can improve the slump loss of concrete and even improve its workability, but it will correspondingly increase the cost of admixture compounding. In some regions, the selling price of admixtures is very low, and adding slow-release mother liquor can lead to no profit for admixtures. The mixing plant does not want to increase the purchase price of additives, and the additive company does not want to reduce profit margins. The injured were the staff who were stuck in their technical positions.